I am a die-hard NFL and college football fan. When I am in Europe, I get up at 1.45am on Friday mornings to watch Thursday Night Football. For the last decade, I have watched days 1 and 2 of every NFL draft live.
And last month, in the midst of COVID-19, the world saw the first ever virtual NFL draft. What a logistical masterpiece it was.
I admit, creating a segway from the NFL draft to construction CO2 emissions feels like a stretch. But hear me out.
One thing I appreciate every year during the draft is the extraordinary accomplishment it is for these young players to make the cut into the NFL. Just 0.16% of every graduating class of high school players makes it into the NFL. Think about this: the decisions they need to take to get into the NFL have not happened this year. Nor last year. They happened 15-20 years before, when they were aged 4–5, adopting a training and diet regimen that would prepare them for the NFL.
Let’s transfer that into construction emissions. The discussions we observe are centered around having to replace bad construction materials to solve emissions.
The problem with that is: all decisions related to which materials and how much of those materials get used are not taken during construction. The materials decisions are taken months or even years earlier during the architecture and engineering phases. In spite of that, many folks still discuss CO2 in relation to materials during the construction phase. Herd instinct, I guess.
Or to put it in a visual that gamers from the 1980s will appreciate:
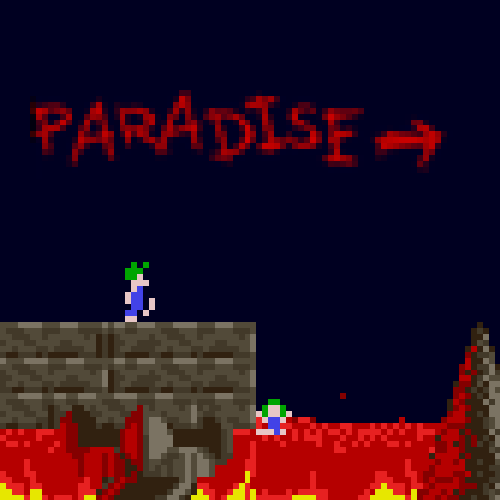
So against the grain, we asked ourselves: can we prove that the issue is not the materials themselves, but the decision and selection of materials during pre-construction? Let’s see here.
1/ So how bad is it, really? For most questions in life, the answer depends on who you ask. For this question, it does not. Uniformly, numbers suggest that less than 30% of all projects over the past 3 years have come within +- 10% of the budget. In other words: 70% of projects are at least more than 10% inaccurate. Studies show regular inaccuracies up to +160%. Everybody has a favorite screwed up project in their hometown. Talking about bad planning, huh.
2/ We found a mind-blowing correlation between cost overruns and the effort invested in pre-construction planning. We have meta-analyzed various recent studies on the subject. What emerged was the following picture — on the horizontal we mapped the projects, on the vertical we mapped the cost over- and underruns (yes, underruns also occur from time to time…).. Check it out …
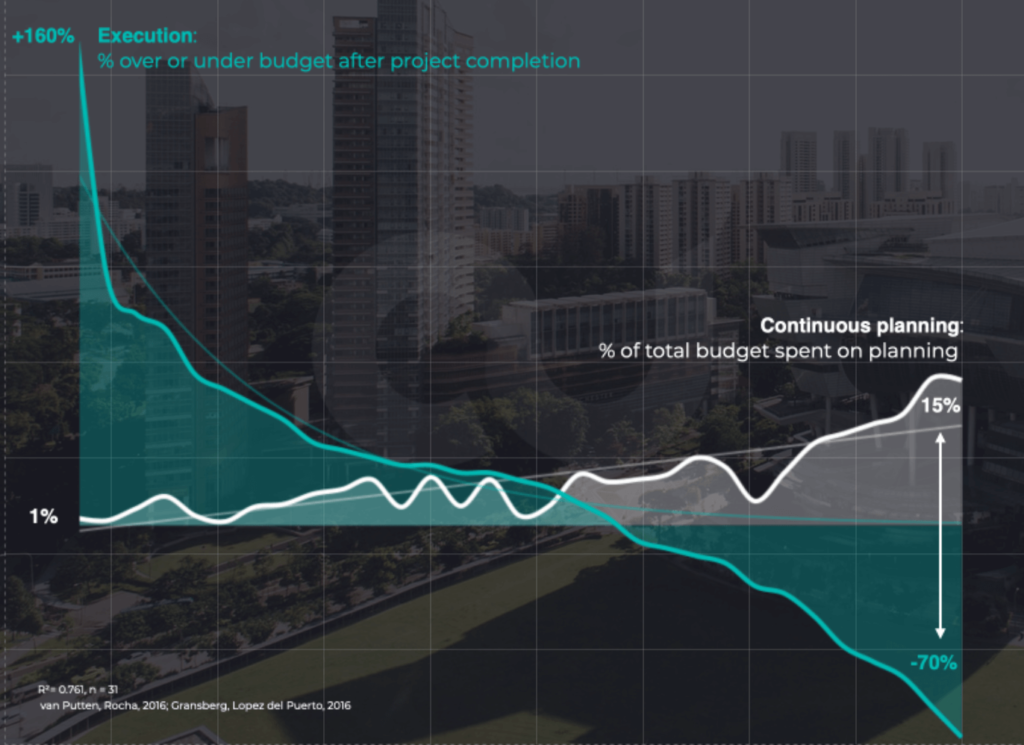
3/ Now, the impact of bad planning on cost is intuitive. What about the impact of bad planning on CO2 emissions, though? Studies show that during pre-construction on average 140–380 design conflicts and omissions are made. If you avoid a portion of those planning errors just by applying BIM, studies find that huge improvements can occur. Eg. 96% of concrete waste can be avoided (96%… blows my mind). And: We found various reputed studies on how much CO2 can be avoided by more efficient engineering — the lower end numbers were 2.5+ kg of cement per m2 floor area built, 6.7+ kg of steel and another 6.5+kg of other mined materials (copper, bauxite).
4/ Ergo: If you build a new Taipei 101 with 412’500 m2 of floor area, you could save 31+ million kg of CO2 just through better pre-construction planning on that one building. That is the equivalent of 6’700 brand-new passenger vehicles driving 10’000 miles per year.
5/ Fine, so now we know that on a single project, there is some lever. But what about the global scale? Construction and the extraction of construction materials account for 17% of global CO2 emissions. 51% of the global industrial carbon emissions come from the processing of four key materials: steel (25%), cement (19%), plastic and aluminium (3%). Construction accounts for more than 50% of world steel demand (if you’re like me, you might have thought automotive was the largest consumer — uh-uh). This all happens before construction has actually begun. Collectively, concrete, steel and bricks generate 315 MT of waste per year globally. Our point here: huge lever on optimizing your architectural material mix before you even begin construction on a global scale.
6/ Now, the good news is: we are seeing innovative building materials taking encouraging steps more recently. We are seeing founders building around new, more sustainable materials, eg. waste polymer materials and cross-laminated bamboo. But: the supply of these more sustainable materials is just not yet large enough to cover the massive construction demand. In the US for instance, 90% of the timber harvested already comes from one third of the timberland base. In other words: if we increase our timber demand exponentially to use in construction, we’ll have no forests left. Not a great scenario.
7/ And: concrete is just a massively easy-to-deploy structural material to bear static loads. While we see encouraging steps where sustainable materials are being increasingly used for renovation and residential building projects, projects which require complex structural loads — such as public infrastructure — will require more pre-construction innovation for us to reduce CO2. Example: in India, residential buildings — which tend to have low structural requirements — currently account for only 20% of total construction project value. Which means: the other 80% is made up from demand with high static load requirements (infrastructure, mid-rise, high-rise, etc).
8/ So that means: if we want to get CO2 emissions under control, we need to become able to handle high static loads with lower amounts of alternative materials. That is the fundamental crux of the issue. Many of the architects and engineers we speak to see auto-generative design (AGD) not primarily as an automation tool — they see AGD as a simulation tool to engineer high static load structures to reduce the amount of eg. concrete needed, and to reduce the amount of omissions and errors to reduce waste. We agree.
9/ That’s great. But not the full picture just yet. The old adage is: you cannot control what you don’t measure. The same is true for optimizing CO2 during pre-construction. We observe a lack of transparent benchmarks to compare a project’s CO2 emissions against. This is especially important since the CO2 footprint is a result of highly interdependent engineering and planning during pre-construction. How will my CO2 footprint be impacted if I redesign this floor? How will it impact my material choice? And even more complex, how will it impact my emissions from logistics? Benchmarks are the final missing piece to complement AGD + BIM + alternative materials.
10/ As investors, we doubt that associations or government bodies will move fast enough to provide the benchmarks — we are excited about founders tackling the benchmark issue from (1) the interop/API angle and (2) highly advanced multi-parameter optimization and simulated design during the architecture and engineering stages.
To paraphrase an old piece of VC wisdom on this issue:
‘Come for the interoperability, stay for the transparency’
So, to summarize:
Bad: CO2 comes from waste that could have been avoided by better planning.
Bad: CO2 comes from using more high-emitting materials than required to cover static loads.
Way forward: AGD/multi-parameter optimization + BIM + alternative materials + benchmarks via interop/APIs.
In our mind: the issue is not the materials themselves, but the decision and selection of materials during pre-construction.
To all founders attacking CO2 during the architecture and engineering phases of construction: let’s go. We’ve got it.
Sources:
- Researchgate.net, 2020
- Worldsteel, 2019
- Plangrid, 2019
- KPMG, 2019